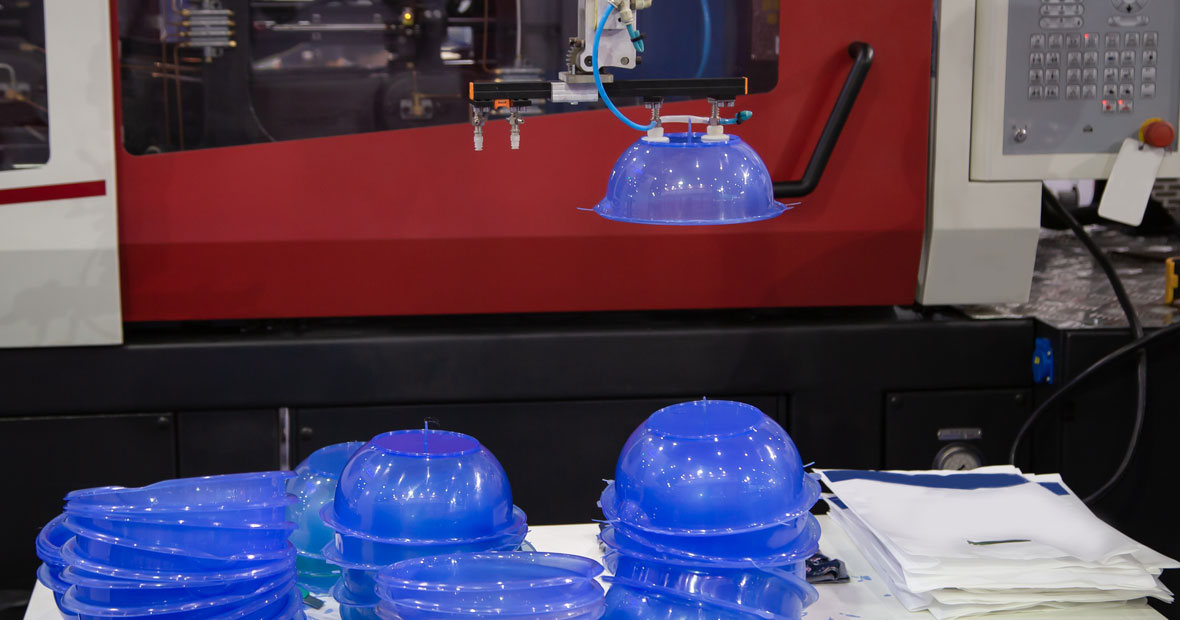
L'art du thermoformage plastique, vieux comme le monde, continue de surprendre par son omniprésence. Sa flexibilité et sa facilité d'utilisation le rendent attrayant pour diverses industries, allant de l'alimentaire au médical, en passant par l'automobile et même l'aérospatiale. Jamais auparavant une technique n'avait été aussi polyvalente, se réinventant constamment pour répondre aux exigences de notre époque. Ce texte révèle certaines des nombreuses applications du thermoformage plastique, démontrant son rôle essentiel dans notre quotidien.
Applications du thermoformage plastique dans l'emballage alimentaire
Dans le domaine de l'emballage alimentaire, le thermoformage plastique trouve de nombreuses utilités. Il s'agit d'un processus qui implique l'utilisation d'une feuille de plastique chauffée jusqu'à devenir malléable, puis moulée pour obtenir la forme souhaitée. Les emballages alimentaires bénéficient grandement de cette technique.
Les barquettes pour fruits et légumes sont fabriquées par thermoformage. Cette technique permet de créer des emballages sur mesure qui protègent le produit tout en permettant sa visualisation. Dans le même ordre d'idée, les gobelets et couvercles en plastique, adaptés aux boissons chaudes et froides, sont produits par ce processus.
En outre, les boîtes transparentes utilisées pour l'emballage des produits de boulangerie et de pâtisserie sont le résultat du thermoformage. Cette technique met en valeur le produit tout en assurant sa protection. De la même façon, l'emballage sous vide pour viandes et poissons est conçu par thermoformage. Cela permet d'allonger la durée de conservation des aliments frais.
Le thermoformage est aussi utilisé pour développer des plateaux pour repas prêts-à-manger. Cette technique offre la possibilité de produire des compartiments adaptés aux différents composants d'un repas. Dans le domaine des produits laitiers, comme les yaourts et fromages, le thermoformage est utilisé pour créer des contenants adaptés qui conservent la fraîcheur et la qualité du produit.
Le plastique thermoformage est largement utilisé dans l'industrie de l'emballage alimentaire. Son faible coût et sa capacité à être moulé en différentes formes en font un choix populaire pour de nombreuses applications. La matière plastique, une fois thermoformée, offre une qualité et une polyvalence inégalées, ce qui explique en grande partie son utilisation répandue.
Utilisation du thermoformage plastique dans le secteur médical
Au cœur du secteur médical, le thermoformage plastique s'impose par sa polyvalence. Ses applications sont nombreuses, allant de la fabrication de boîtiers pour équipements médicaux à la création d'emballages stériles pour instruments chirurgicaux. Le thermoformage de polycarbonate, matériau utilisé pour sa résistance aux chocs et sa précision de forme, est particulièrement apprécié. En effet, il permet de produire des boîtiers de haute qualité, capables de protéger efficacement les équipements sensibles.
Dans le domaine de l'emballage, le thermoformage plastique fait preuve d'une efficacité remarquable. Les blisters et les emballages stériles qu'il permet de réaliser sont dotés d'une précision et d'une résistance inégalées, garantissant ainsi la sécurité des instruments chirurgicaux. Le matériau thermoplastique utilisé offre un avantage du thermoformage indéniable : la légèreté du produit final.
Par ailleurs, dans la conception de prothèses externes sur mesure et de composants pour dispositifs d'imagerie médicale, l'utilisation de ce procédé est primordiale. Il permet d'obtenir une précision de forme irréprochable, tout en assurant une résistance optimale aux contraintes mécaniques. L'association du thermoformage avec l'impression 3D ouvre de nouvelles perspectives, notamment dans la création de modèles anatomiques complexes pour la formation médicale et la planification chirurgicale.
Le thermoformage plastique dans l'industrie automobile
Le rôle du plastique dans l'industrie automobile a évolué au fil du temps. Le thermoformage est l'une des principales techniques utilisées dans ce secteur, permettant la création de composants intérieurs et extérieurs esthétiques et résistants. Grâce à sa haute résistance et sa capacité à prendre des formes diverses, le plastique thermoformé trouve sa place dans la production de tableaux de bord et garnitures de porte.
Le processus de fabrication est aussi orienté vers l'extérieur des véhicules. Les pare-chocs aérodynamiques et les carénages légers sont fabriqués en utilisant cette technique. Le thermoformage garantit une flexibilité de forme, un atout majeur pour l'industrie automobile. La légèreté du matériau est un autre facteur clé, particulièrement pour les bacs de batteries destinés aux véhicules électriques. Ces pièces nécessitent des plastiques thermoformés pour leur résistance chimique.
Les éléments optiques des véhicules, tels que les phares et les feux, sont d'autres exemples d'applications du thermoformage. La précision et la clarté du matériau sont essentielles pour ces composants. Par ailleurs, le thermoformage est le choix privilégié pour le développement rapide de prototypes, permettant de réduire les coûts et les délais de l'outillage par rapport au moulage par injection.
Cette technique permet de produire des pièces avec des finitions complexes et des détails précis. Ce qui optimise l'assemblage et la qualité finale du véhicule. Ainsi, le thermoformage se positionne comme une alternative efficace au formage sous pression et au moulage par injection, offrant des avantages considérables contre le moule traditionnel, notamment en termes de coûts et de temps de production.
Développements récents du thermoformage plastique dans l'aérospatiale
Le domaine de l'aérospatiale connaît des avancées importantes en matière de thermoformage plastique. L'utilisation de plastiques haute performance pour la conception des composants intérieurs des avions a conduit à une amélioration notable de la résistance et à une réduction du poids. Grâce à des techniques de formage sous vide, la production de pièces aérospatiales complexes à partir de matériaux résistants à la chaleur est devenue possible. Ceci est dû au développement de procédés de thermoformage innovants.
Un autre progrès notable est l'innovation dans les formes de moules pour le thermoformage. Ces formes permettent la production rapide de composants aérospatiaux en série, réduisant ainsi les coûts et les délais de fabrication. Par ailleurs, l'application du thermoformage dans la fabrication de fenêtres d'avion résistantes aux impacts et aux variations de pression est une autre avancée considérable.
Le thermoformage plastique est utilisé pour créer des revêtements aérodynamiques qui améliorent l'efficacité énergétique des aéronefs. La structure des satellites bénéficie de l'intégration de matériaux composites thermoformés, offrant une résistance et une légèreté optimales dans l'environnement spatial. La technologie du thermoformage continue donc de jouer un rôle clé dans le développement de l'aérospatiale.